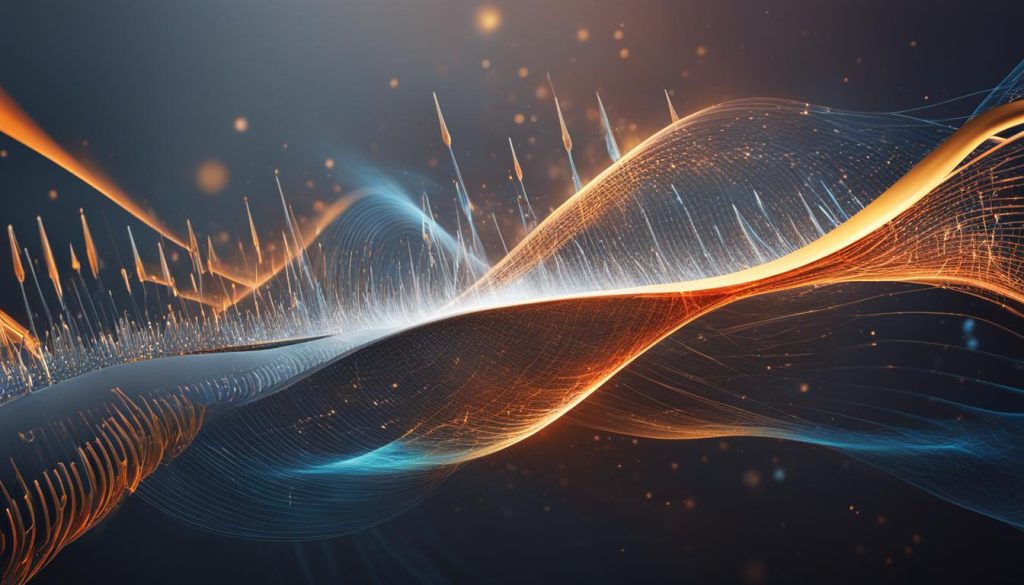
When it comes to the fascinating world of musical instruments, the tuning fork holds a unique place.
Have you ever wondered how does a tuning fork works? Let’s unravel the mechanics behind the tuning fork and explain how it operates.
When a tuning fork is struck, its two prongs, known as “tines,” vibrate back and forth several hundred times per second.
These rapid vibrations create sound waves as the tines push surrounding air molecules together (compressions) and then pull them apart (rarefactions).
It is this back-and-forth motion that generates the characteristic sound of the tuning fork.
The frequency of these vibrations determines the pitch of the note produced by the tuning fork.
Simply put, the faster the vibrations, the higher the pitch, and vice versa. So, a tuning fork works by converting mechanical energy into sound energy through the rapid vibrations of its prongs.
Content
- 1 The Science Behind Tuning Fork Vibrations
- 2 Practical Applications of Tuning Forks
- 3 The Construction of a Tuning Fork
- 4 Adjusting the Pitch of a Tuning Fork
- 5 Historical Development of Tuning Forks
- 6 Tuning Forks in Everyday Life
- 7 The Physics of Sound Waves
- 8 The Relationship Between Frequency and Pitch
- 9 Physical Characteristics and Tuning Fork Frequency
- 10 Source Links
The Science Behind Tuning Fork Vibrations
When it comes to understanding how does a tuning fork work, it’s important to delve into the science behind their vibrations.
Tuning forks consist of two elastic metal prongs that oscillate back and forth, creating rapid vibrations.
As these prongs move, they generate patterns of high-pressure compressions and low-pressure rarefactions in the surrounding air, which ultimately form sound waves.
The frequency or pitch of the sound produced by a tuning fork depends on the speed of these vibrations.
The size and material of the prongs can also impact the vibrations and consequently the pitch.
This phenomenon is known as resonance, where an object vibrates at its natural frequency when excited by a similar frequency. In the case of tuning forks, the rapid oscillations of the prongs result in the production of distinct tones.
Understanding the physics of tuning fork vibrations is crucial, as it allows us to appreciate the foundational principles behind the production of sound waves.
By studying the science behind tuning fork mechanics, we gain insights into how these instruments can be utilized in a variety of practical applications, from sound therapy to diagnostic tests in medical fields.
Tuning Fork Physics and Resonance
The vibration of tuning forks is governed by the laws of physics. When a tuning fork is struck, it possesses potential energy, which is converted into kinetic energy as the prongs begin to vibrate.
The mechanical vibrations of the prongs displace air molecules, creating regions of compression and rarefaction that propagate as sound waves. The frequency of these vibrations determines the pitch of the note produced.
Resonance plays a significant role in tuning fork physics. When a tuning fork is excited by an external force, it vibrates at its natural frequency.
This occurs because the fork’s prongs are in resonance with the force applied, resulting in sustained oscillations.
The prongs continue to vibrate until energy is either dissipated through air resistance or transferred to another object through contact, causing it to vibrate with the same frequency.
The Relationship Between Prong Characteristics and Pitch
The physical characteristics of tuning fork prongs, such as their length, thickness, and material, directly impact the frequency and pitch of the sound produced.
Shorter and thinner prongs vibrate at higher frequencies, producing higher-pitched sounds.
On the other hand, longer and thicker prongs vibrate at lower frequencies, resulting in lower-pitched sounds.
Furthermore, the material chosen for the prongs can also influence the pitch of the tuning fork.
Dense metals like copper and steel tend to produce higher-pitched sounds, while softer metals like brass create lower-pitched tones.
Adjusting these physical characteristics during the manufacturing process allows for the selection and fine-tuning of specific pitches for different types of tuning forks.
The science behind tuning fork vibrations provides a fundamental understanding of how these instruments create sound waves and produce distinct pitches.
By exploring the physics and principles governing tuning forks, we can better appreciate their role in various fields and applications.
Practical Applications of Tuning Forks
Tuning forks have proven to be useful beyond their traditional role in musical tuning. They have found practical applications in various fields, including sound therapy and healthcare.
Sound Therapy:
In sound therapy, tuning forks are used to create harmonic vibrations that can resonate with the body.
These vibrations are believed to promote relaxation and healing. By using specific frequencies and techniques, sound therapists aim to restore balance and harmonize the body’s energy.
Medical Applications:
Tuning forks are also used in diagnostic tests to assess hearing loss. The Weber and Rinne tests, for example, rely on the vibrations of tuning forks.
By placing a vibrating fork on specific points, medical practitioners can determine if there is a hearing impairment or potential bone fracture.
The vibrations of the tuning fork can be felt through bone conduction, bypassing the middle ear.
Nursing:
In nursing, tuning forks are occasionally used to assess potential bone fractures.
By pressing a vibrating fork against the suspected injured area, nurses can detect any abnormalities or tenderness. This method can provide a quick initial assessment and help guide further medical interventions.
Tuning forks have proven to be versatile tools, extending beyond their primary use in music.
Whether in sound therapy or healthcare, these simple yet effective instruments continue to find practical applications in our everyday lives.
The Construction of a Tuning Fork
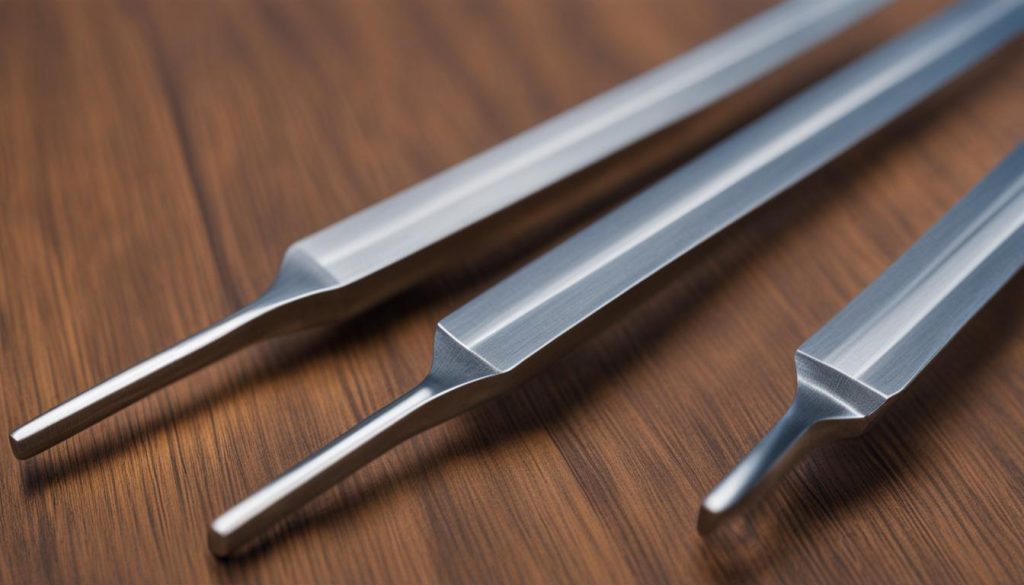
A tuning fork is a simple yet intricate instrument that produces sound through its vibrating prongs.
Let’s take a closer look at the construction of a tuning fork and the materials used in its production.
The basic design of a tuning fork consists of a handle and two prongs or tines. These prongs are made from elastic metal, typically steel, which allows them to vibrate rapidly when struck.
The vibrations of the prongs generate sound waves, producing a pure tone with most of the energy concentrated at the fundamental frequency.
Commercial tuning forks are often tuned to specific frequencies and are commonly made of stainless steel. Stainless steel is chosen for its durability and economic reasons, making it an ideal material for mass production.
The use of stainless steel ensures that the tuning forks can withstand repeated striking while maintaining their accuracy and longevity.
The Construction Materials of Tuning Forks:
Material | Properties |
---|---|
Steel | Durable, elastic, and commonly used in commercial tuning forks. |
Stainless Steel | Resistant to corrosion, making it suitable for long-term use. |
Brass | Softer metal that can produce lower-pitched tones. |
Copper | Dense metal known for producing higher-pitched sounds. |
The choice of materials and their specific properties play a crucial role in the construction of tuning forks, ensuring their functionality and sound quality.
By carefully selecting the appropriate metal and design, tuning forks can be crafted to meet the required frequency and pitch for various applications.
Adjusting the Pitch of a Tuning Fork
Adjusting the pitch of a tuning fork can be achieved by modifying the length, thickness, and material of its prongs.
These factors directly impact the frequency at which the tuning fork vibrates, ultimately determining the pitch of the sound it produces.
Shorter and thinner prongs tend to vibrate at higher frequencies, resulting in a higher pitch. Conversely, longer and thicker prongs vibrate at lower frequencies, producing a lower pitch.
By adjusting the dimensions of the prongs, manufacturers can fine-tune the desired pitch for a specific tuning fork.
The material used to make the tuning fork also plays a significant role in its pitch. Dense metals like copper and steel produce higher-pitched sounds, while softer metals like brass create lower-pitched tones.
Manufacturers can choose the appropriate material based on the desired pitch range for the tuning fork.
Factors Affecting Pitch Adjustments:
- Length of the prongs: Shorter prongs result in a higher pitch, while longer prongs result in a lower pitch.
- Thickness of the prongs: Thinner prongs produce a higher pitch, while thicker prongs produce a lower pitch.
- Material of the prongs: Dense metals like copper and steel produce a higher pitch, while softer metals like brass produce a lower pitch.
By considering these factors and making adjustments during the manufacturing process, tuning fork makers can create forks with different pitches to cater to various musical and scientific applications.
Prong Length | Prong Thickness | Material | Pitch |
---|---|---|---|
Short | Thin | Steel | High |
Long | Thick | Brass | Low |
Historical Development of Tuning Forks
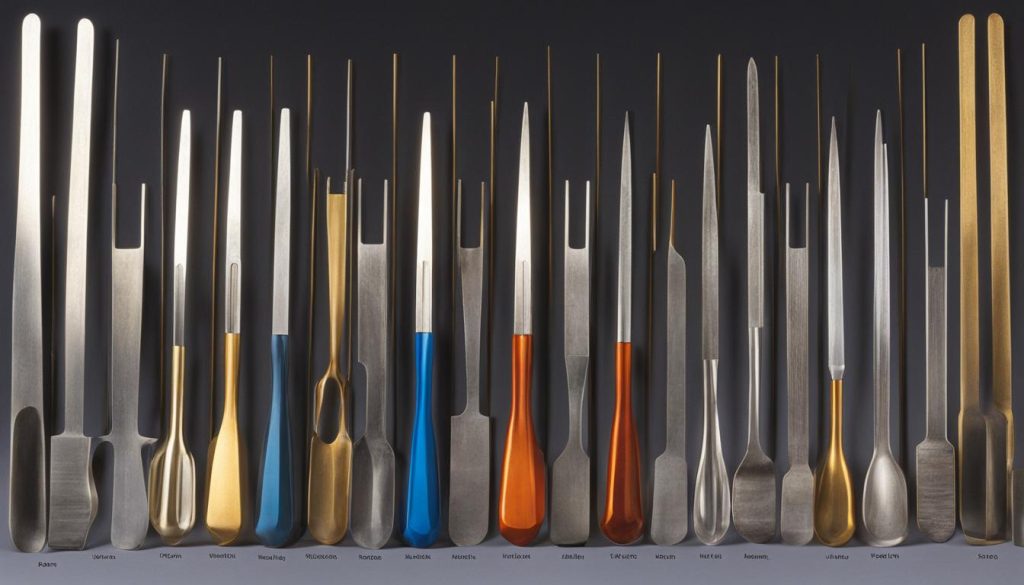
The invention of the tuning fork dates back to 1711 when British musician John Shore created this ingenious device.
Shore, who served as a sergeant trumpeter and lutenist to the royal court, wanted to create a reliable and accurate tool for tuning musical instruments.
His invention marked a significant advancement in the field of music and instrument tuning.
Since Shore’s invention, tuning forks have undergone various developments and improvements. Between 1750 and 1820, orchestras used different tuning forks with slightly varying pitches.
These forks were employed as standard pitch references, ensuring that musical instruments were in tune with each other.
Today, the most commonly used standard pitch for tuning forks is A=440 Hz. This pitch has been widely adopted in concert settings, allowing musicians to tune their instruments to a standardized frequency.
The evolution of tuning forks over the centuries has contributed to the precise and harmonious sounds we enjoy in music today.
Year | Key Developments |
---|---|
1711 | John Shore invents the tuning fork |
1750-1820 | Different tuning forks with slightly varying pitches used by orchestras as standard pitch references |
Present | A=440 Hz widely adopted as the standard pitch for tuning forks in concert settings |
Invention of the Tuning Fork
“The tuning fork was invented in 1711 by British musician John Shore, who was a sergeant trumpeter and lutenist to the royal court.”
The invention of the tuning fork by John Shore revolutionized the process of tuning musical instruments. Prior to its creation, musicians relied on their ears and subjective judgments to tune their instruments.
Shore’s invention provided a reliable and consistent tool that allowed for precise tuning.
Tuning Forks in Everyday Life
Tuning forks have become integral to various aspects of everyday life, extending beyond the realms of music and healthcare.
Their reliable and precise vibrations have led to their utilization in a wide range of applications, showcasing their versatility and practicality.
Applications of Tuning Forks in Everyday Life
Application | Description |
---|---|
Radar Gun Calibration | Tuning forks are utilized to calibrate radar guns, ensuring accurate speed measurements for law enforcement and traffic control. |
Gyroscopes | They plays a crucial role in the development of gyroscopes, aiding in the accurate measurement of rotation and navigation in various industries. |
Timekeeping Devices | Quartz crystal resonators, often incorporating tuning forks, are employed in clocks and watches to maintain accurate timekeeping. |
Alternative Therapy Practices | They play a crucial role in the development of gyroscopes, aiding in the accurate measurement of rotation and navigation in various industries. |
These applications highlight the widespread integration of tuning forks into our everyday lives.
From law enforcement to navigation, timekeeping to wellness practices, tuning forks continue to prove their value and effectiveness.
Their ability to produce consistent vibrations makes them an essential tool in various fields, enhancing precision and ensuring optimal performance.
It is fascinating to see how such a seemingly simple device can have such diverse applications, impacting our lives in ways we may not even realize.
From aiding in accurate measurements to promoting well-being, they have truly transcended their musical origins.
The Physics of Sound Waves
Understanding the physics of sound waves is essential in comprehending how tuning forks work.
Sound waves are classified as longitudinal waves, where particles of the medium (usually air) vibrate back and forth in the same direction as the energy transport.
As a tuning fork’s prongs vibrate, they create compressions and rarefactions in the air, resulting in alternating areas of high and low pressure.
These pressure variations form the sound waves that propagate through the air, carrying the energy of the vibrations from one location to another without physically displacing the particles themselves.
Sound waves possess several properties that influence how we perceive and interpret them. One fundamental property is frequency, measured in hertz (Hz), which represents the number of vibrations or cycles per second.
The frequency of a sound wave directly corresponds to the pitch we perceive. Higher frequencies result in higher-pitched sounds, while lower frequencies produce lower-pitched sounds.
For example, a tuning fork vibrating at 4000 Hz would create a sound similar to the top key on a piano, while one vibrating at 28 Hz would mimic the lowest key.
Another characteristic of sound waves is amplitude, which determines the volume or loudness of a sound. Amplitude refers to the maximum displacement of particles in a medium from their equilibrium position during the passage of a sound wave.
A higher amplitude results in a more intense sound, while a lower amplitude produces a softer sound. Additionally, sound waves also possess a phase, which refers to the position of a particle in its vibratory motion at a specific instant in time.
Table: Properties of Sound Waves
Property | Description |
---|---|
Frequency | The number of vibrations or cycles per second, determining the pitch of a sound. |
Amplitude | The number of vibrations or cycles per second, determines the pitch of a sound. |
Phase | The position of a particle in its vibratory motion at a specific instant in time. |
Understanding the properties of sound waves is crucial in various fields, including music, engineering, and medicine.
By deciphering the intricate workings of sound waves, we can better appreciate how tuning forks and other sound-producing objects function.
The Relationship Between Frequency and Pitch
When it comes to understanding the pitch of a tuning fork, it is essential to consider its frequency.
The frequency refers to the number of vibrations or cycles per second and is measured in hertz (Hz).
The relationship between frequency and pitch is straightforward: a higher frequency corresponds to a higher pitch, while a lower frequency corresponds to a lower pitch.
A tuning fork with faster vibrations will have a higher frequency, producing a higher-pitched sound. On the other hand, a fork with slower vibrations will have a lower frequency, resulting in a lower-pitched sound.
For instance, fork vibrating at 4,000 Hz will mimic the top key on a piano, while one vibrating at 28 Hz will mimic the lowest key.
To help illustrate this relationship, consider the following table:
Tuning Fork Frequency (Hz) | Pitch |
---|---|
4,000 | Top key on a piano |
440 | A common standard pitch |
28 | Lowest key on a piano |
As you can see, the frequency of the tuning fork directly correlates to the pitch of the sound it produces.
Understanding this relationship is crucial for musicians, scientists, and anyone interested in the mechanics of sound.
Physical Characteristics and Tuning Fork Frequency
When considering the frequency of a fork, there are several physical characteristics that come into play.
These factors include the length, mass, material, and cross-sectional area of the tuning fork’s prongs.
Each of these elements contributes to the unique frequency at which the tuning fork vibrates.
Calculating the frequency of a fork involves using a mathematical equation that takes into account these physical characteristics.
The equation incorporates terms such as Young’s modulus of elasticity, density, and second moment of area.
By inputting the specific values for each characteristic, it is possible to determine the frequency at which the tuning fork will vibrate.
Commercially available forks are carefully manufactured to ensure they produce the correct pitch at a standard temperature, typically around 20°C or 68°F.
However, it’s important to note that the pitch of a tuning fork can slightly vary with temperature due to changes in the modulus of elasticity of the material.
Therefore, it’s essential to take temperature into consideration when working with tuning forks for precise measurements or applications.